Profiling small laser beams and measuring the beam size (or mode field diameter) can be a serious challenge. But it’s critical to measure, especially in such applications as fiber optic coupling efficiency, defect scanning, optical design and optical fabrication process control.
Challenges with profiling very small laser beams
- Camera pixels are usually 3-10 μm, so the resolution isn’t good enough to measure such small beams.
- Need very high precision of the BP setup.
- Typically very divergent.
There are two possible solutions: Near-Field Profiling (NFP) and Far-Field Profiling (FFP).
Near-Field Profiling
Overview – Use strong optics (microscope objective) to expand the beam as necessary and the profile as usual.
Pros – Simple, intuitive
Cons – Very sensitive to optical/mechanical setup (small changes in the original beam lead to large inaccuracies in the profile measured)
Tip – Any filter attenuators should be placed after the objective, on the larger, collimated beam. If they are placed on the original small beam, the high power/energy densities could cause thermal lensing (and distortion due to high divergence in filter).
Far-Field Profiling
Overview – Profile the beam in the far field*, then transfer the far-field distribution into the near-field.
Pros – No attenuation necessary, not sensitive to mechanical setup (and therefore very repeatable), typically faster than NFP
Cons – Beam size might be too large to profile with typical cameras.
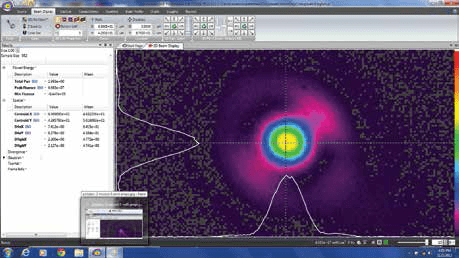

Read Derrick Peterman’s full article for more information.
Leave a Reply
Your email address will not be published. Required fields are marked *