In-Process vs. At-Process Monitoring: Which approach is best for laser performance? As Industry 4.0 reshapes manufacturing, understanding these methods can help you boost efficiency.
Discover the key differences and find out which monitoring strategy is right for your operations.
The modern manufacturing landscape is increasingly driven by data and automation as Industry 4.0 takes hold. This shift is transforming how we handle laser processing in industries where precision and efficiency are paramount. Monitoring laser performance is a critical aspect of ensuring the quality and reliability of laser-based processes. However, choosing the right monitoring approach can be challenging, with each method offering its unique benefits and limitations.
In-Process vs. At-Process Monitoring
In industrial laser processing, operators typically have two main options: In-Process Monitoring and At-Process Monitoring. In-Process Monitoring enables operators to check laser parameters while the system is running, offering immediate feedback and on-the-fly adjustments. However, it often captures only a fraction of the data, which may miss some critical issues.
On the other hand, At-Process Monitoring is conducted between production runs or during scheduled downtimes. This approach provides a comprehensive snapshot of the system’s performance but requires taking the laser out of production temporarily, which can impact efficiency and cost.
Choosing the Right Approach
In the article “In-Process vs At-Process Monitoring in Industrial Laser Processing,” John McCauley explores these two monitoring approaches, offering insights that can help you determine the most effective way to measure and maintain laser performance. Whether you prioritize real-time feedback or thorough, post-process analysis, understanding these methods will enable you to optimize your laser processing systems for reliability and efficiency.
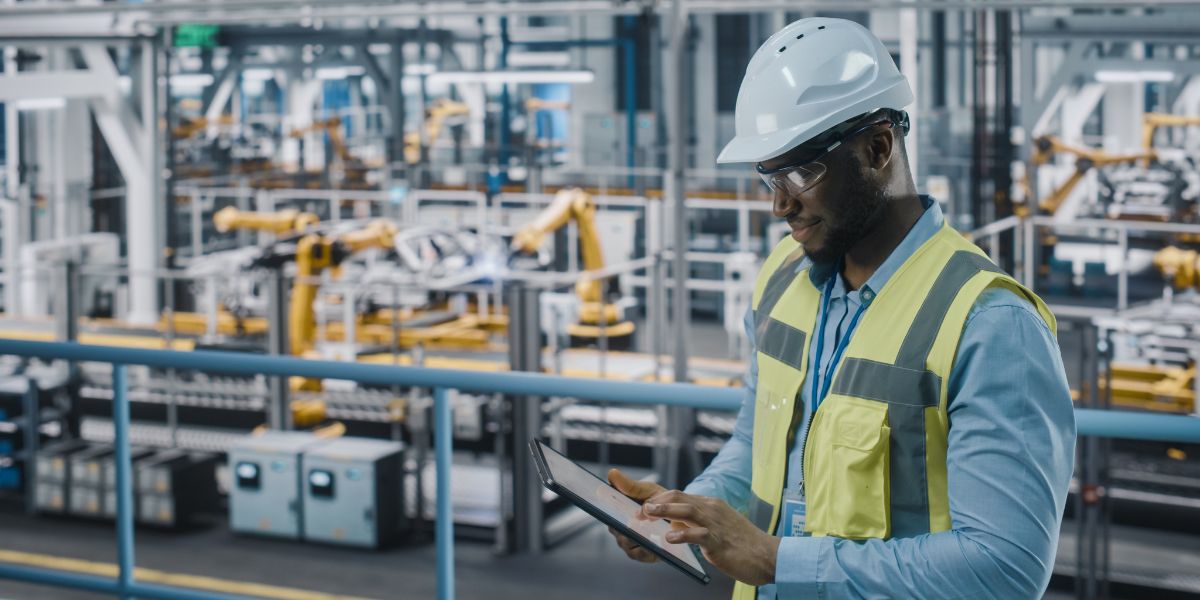
Leave a Reply
Your email address will not be published. Required fields are marked *